Результат выполнения конструкторско-технологической разработки.
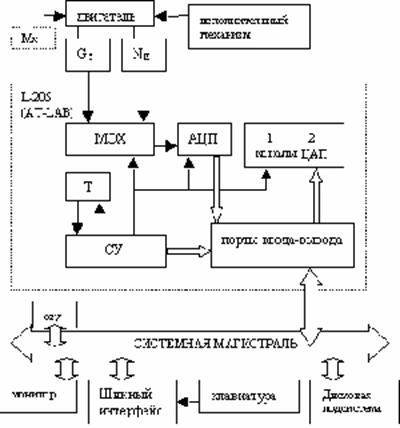
Предлагаемое устройство относится к системам автоматического управления, используемым для автоматического поиска наивыгоднейшего режима работы объекта и перенастройки его на этот режим. Существуют различные типы средств автоматического регулирования эксплуатационных режимов работы машинно-тракторного агрегата (МТА), выходными параметрами которых являются такие энергетические показатели, как эффективная мощность двигателя и расход топлива, по величине которых можно с достаточной точностью контролировать эксплуатационные режимы работы МТА, соответственно при максимальной производительности и минимальных затратах. Использование ЭВМ в устройстве автоматического регулирования нагрузочных режимов работы МТА позволяет выбирать водителю оптимальный нагрузочный режим работы, соответствующий максимальной производительности МТА или минимальным эксплуатационным затратам денежных средств, приходящихся на единицу выработки. На рис. 1 представлена структурная схема устройства автоматического регулирования нагрузочных режимов работы МТА. Оптимизация нагрузочных режимов достигается регулированием оборотов двигателя. Связь ЭВМ с датчиками двигателя и исполнительным механизмом устанавливается методом дифференциального включения, основанного на применении прямых систем связи, так называемых интерфейсов, включаемых непосредственно в системную магистраль компьютера. Используемый в работе интерфейс состоит из: аналого-цифрового преобразователя (АЦП); мультиплексора аналоговых сигналов (mux), устанавливаемого на входе АЦП; программируемого таймера (Т); цифро-аналогового преобразователя (ЦАП); системы управления (СУ); портов ввода-вывода, позволяющих компьютеру получать информацию с датчиков двигателя и управлять исполнительным механизмом. Сигналы с датчиковgт и ne поступают на контроллер. Контроллер представляет собой электронный модуль (плат l-205), вставляемый в компьютер, разъемно-совместимый сibm pc, на любое из свободных платомест. Вводимые аналоговые сигналы для аналого-цифрового преобразования. Полученные после преобразования 10 информационных бит и 4 бита номера канала запоминаютсяв регистрах, после чего за два цикла в режиме прямого доступа к памяти (ПДП) вводятся в оперативную память компьютера (ОЗУ). Скорость ввода данных задается путем программирования таймера. Обработав полученную с датчиков информацию, компьютер в зависимости от выбранного оптимального нагрузочного режима работы, вырабатывает управляющий сигнал. Система управления переключает каналыmuxи осуществляет запрос в режиме ПДП о готовности данных, поступающих на каналы ЦАП, откуда цифровой управляющий сигнал, преобразованный в аналоговую форму, поступает в канал управления исполнительного механизма, в качестве которого используется шаговый двигатель, осуществляющий перемещение рейки топливного насоса двигателя.